ရေခံနိုင်ရည် ညံ့ဖျင်းခြင်း၊ မျက်နှာပြင် မညီညာခြင်း၊ အမှုန့်ပါဝင်မှု မြင့်မားခြင်းနှင့် အရှည်မညီမညာ ဖြစ်နေပါသလား။ရေနေအစာထုတ်လုပ်မှုတွင် အဖြစ်များသောပြဿနာများနှင့် တိုးတက်မှုအစီအမံများ
ကျွန်ုပ်တို့၏နေ့စဉ် ရေနေအစာထုတ်လုပ်ရာတွင် ကဏ္ဍပေါင်းစုံမှ ပြဿနာအချို့ကို ကြုံတွေ့ခဲ့ရသည်။ဤသည်မှာ အောက်ပါအတိုင်း လူတိုင်းနှင့် ဆွေးနွေးရန် ဥပမာအချို့ဖြစ်သည်။
၁၊ ဖော်မြူလာ
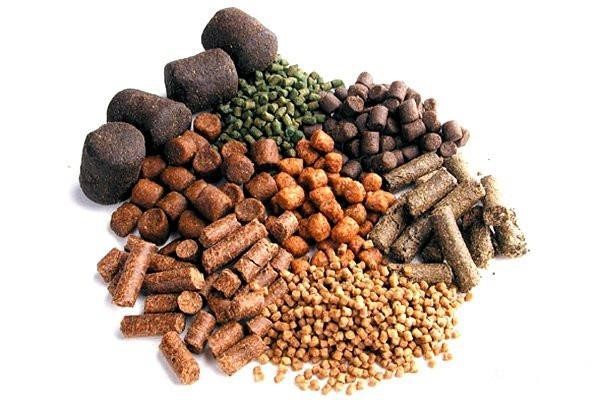
1. ငါးအစာ၏ ဖော်မြူလာဖွဲ့စည်းပုံတွင်၊ အမျှင်ကြမ်းနှင့် အမျှင်ဓာတ်ပါဝင်သည့် ကြမ်းစေ့စေ့၊ ချည်ညက်စသည်တို့ကဲ့သို့သော အစားအစာကုန်ကြမ်း အမျိုးအစားများ ပိုများပါသည်။အချို့သော ဆီစက်ရုံများတွင် ခေတ်မီနည်းပညာများ ရှိပြီး အခြေခံအားဖြင့် ဆီခြောက်ကို ပါဝင်မှုနည်းသော ကြော်သည်။ထို့အပြင် ဤကုန်ကြမ်းအမျိုးအစားများသည် ထုတ်လုပ်မှုတွင် အလွယ်တကူ စုပ်ယူနိုင်ခြင်းမရှိသောကြောင့် granulation တွင် များစွာသက်ရောက်မှုရှိသည်။ထို့အပြင် ဝါဂွမ်းညက်သည် ထိရောက်မှုကို ထိခိုက်စေသော ကြိတ်ချေရန် ခက်ခဲသည်။
2. ဖြေရှင်းချက်- မုဒုံကိတ်မုန့်ကို အသုံးပြုမှု မြင့်တက်လာပြီး ဆန်ဖွဲကဲ့သို့သော အရည်အသွေးမြင့် ဒေသထွက်ပစ္စည်းများကို ဖော်မြူလာတွင် ထည့်သွင်းထားသည်။ထို့အပြင် ဖော်မြူလာ၏ 5-8% ခန့်ပါဝင်သည့် ဂျုံကို ထည့်သွင်းထားသည်။ချိန်ညှိမှုအားဖြင့်၊ ၂၀၀၉ ခုနှစ်တွင် granulation effect သည် အတော်လေး စံပြဖြစ်ပြီး တစ်တန်လျှင် အထွက်နှုန်းလည်း တိုးလာသည်။၂.၅ မီလီမီတာ အမှုန်အမွှားများသည် ၈ တန်မှ ၉ တန်ကြားရှိပြီး ယခင်နှင့် နှိုင်းယှဉ်ပါက ၂ တန်နီးပါး တိုးလာပါသည်။အမှုန်များ၏ အသွင်အပြင်သည်လည်း သိသိသာသာ တိုးတက်လာသည်။
ထို့အပြင်၊ မညက်တညက်ညက်ညက်ညက်ညက်၏ ထိရောက်မှုကို မြှင့်တင်ရန်၊ မကြိတ်မီ 2:1 အချိုးဖြင့် ကောက်ညှင်းစေ့ကို ရောမွှေပါ။ပိုမိုကောင်းမွန်လာပြီးနောက်၊ ကြိတ်ချေမှုနှုန်းသည် အခြေခံအားဖြင့် မုန်ညှင်းစေ့၏ ကြိတ်ချေမှုအရှိန်နှင့် တန်းတူဖြစ်သည်။
၂၊ အမှုန်များ၏မျက်နှာပြင်မညီညာ
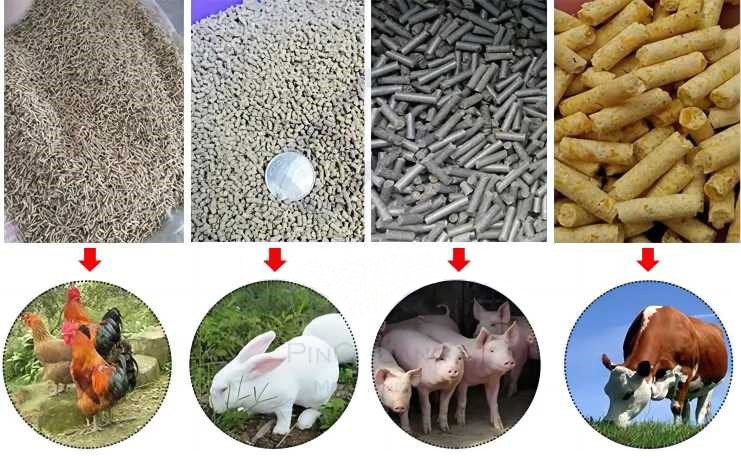
1. ၎င်းသည် ကုန်ချော၏ အသွင်အပြင်အပေါ်တွင် များစွာသက်ရောက်မှုရှိပြီး ရေထဲသို့ထည့်လိုက်သောအခါတွင် ၎င်းသည် ပြိုကျနိုင်ခြေရှိပြီး သုံးစွဲမှုနှုန်းနည်းပါးသည်။အဓိကအကြောင်းရင်းမှာ-
(၁) ကုန်ကြမ်းများကို ကြမ်းလွန်းစွာ ကြိတ်ချေပြီး အပူပေးသည့် လုပ်ငန်းစဉ်တွင် ၎င်းတို့သည် အပြည့်အဝ ရင့်ကျက်ပြီး ပျော့ပျောင်းမသွားဘဲ မှိုတွင်းများကို ဖြတ်သန်းသည့်အခါ အခြားကုန်ကြမ်းများနှင့် ကောင်းစွာ ပေါင်းစပ်မရနိုင်ပါ။
(၂) ဖိုက်ဘာကြမ်းပါဝင်မှု မြင့်မားသော ငါးအစာဖော်မြူလာတွင် ကုန်ကြမ်းထဲတွင် ရေနွေးငွေ့ပူဖောင်းများ ပါဝင်နေခြင်းကြောင့် အဆိုပါပူဖောင်းများသည် မှိုအတွင်းပိုင်းနှင့် အပြင်ဘက်အကြား ဖိအားကွာခြားမှုကြောင့် ကွဲထွက်ခြင်း၊ အမှုန်များ၏မျက်နှာပြင်မညီမညာဖြစ်လာသည်။
2. ကိုင်တွယ်ဆောင်ရွက်မှုများ-
(၁) ကြိတ်ခွဲခြင်းလုပ်ငန်းစဉ်ကို စနစ်တကျ ထိန်းချုပ်ပါ။
လက်ရှိတွင်၊ ငါးအစာထုတ်လုပ်ရာတွင် ကျွန်ုပ်တို့၏ကုမ္ပဏီသည် 1.2mm ဆန်ခါမိုက်ခရိုမှုန့်ကို အစုလိုက်ကုန်ကြမ်းအဖြစ် အသုံးပြုပါသည်။ကျွန်ုပ်တို့သည် ကြိတ်ချေခြင်း၏ ချောမွေ့မှုကို သေချာစေရန် ဆန်ခါအသုံးပြုမှု အကြိမ်ရေနှင့် သံတူ၏ ဝတ်ဆင်မှုအတိုင်းအတာကို ထိန်းချုပ်ပါသည်။
(၂) ရေနွေးငွေ့ဖိအားကို ထိန်းချုပ်ပါ။
ဖော်မြူလာအရ၊ ထုတ်လုပ်စဉ်အတွင်း ရေနွေးငွေ့ဖိအားကို ကျိုးကြောင်းဆီလျော်စွာ ချိန်ညှိပါ၊ ယေဘုယျအားဖြင့် 0.2 ဝန်းကျင်ကို ထိန်းချုပ်ပါ။ငါးအစာဖော်မြူလာတွင် အမျှင်ကြမ်းကုန်ကြမ်း ပမာဏများပြားခြင်းကြောင့် အရည်အသွေးမြင့် ရေနွေးငွေ့နှင့် ကျိုးကြောင်းဆီလျော်သော အပူပေးချိန် လိုအပ်ပါသည်။
၃၊ အမှုန်များ၏ရေခံနိုင်ရည်ညံ့ဖျင်း
1. ဤပြဿနာသည် ကျွန်ုပ်တို့၏နေ့စဉ်ထုတ်လုပ်မှုတွင် အဖြစ်အများဆုံးဖြစ်ပြီး၊ ယေဘူယျအားဖြင့် အောက်ပါအချက်များနှင့် သက်ဆိုင်သည်-
(၁) တိုတောင်းသောအချိန်နှင့် အပူချိန်နိမ့်ခြင်းသည် အပူချိန်မညီညာခြင်း သို့မဟုတ် မလုံလောက်ခြင်း၊ ရင့်မှည့်မှုဒီဂရီနည်းပါးခြင်းနှင့် အစိုဓာတ်မလုံလောက်ခြင်းတို့ ဖြစ်စေသည်။
(၂) ကစီဓာတ်ကဲ့သို့သော ကော်ပစ္စည်းများ မလုံလောက်ခြင်း။
(၃) လက်စွပ်မှို၏ ဖိသိပ်မှုအချိုးသည် အလွန်နည်းသည်။
(၄) ဖော်မြူလာရှိ ဆီပါဝင်မှုနှင့် ဖိုက်ဘာကုန်ကြမ်း အချိုးအစားသည် မြင့်မားလွန်းသည်။
(၅) အမှုန်အမွှားအရွယ်အစားကို ကြိတ်ချေခြင်း ။
2. ကိုင်တွယ်ဆောင်ရွက်မှုများ-
(၁) ရေနွေးငွေ့အရည်အသွေးကို မြှင့်တင်ပါ၊ ထိန်းညှိကိရိယာ၏ ဓားထောင့်ကို ချိန်ညှိပါ၊ အပူခံချိန်ကို တိုးမြှင့်ကာ ကုန်ကြမ်း၏ အစိုဓာတ်ကို သင့်လျော်စွာ တိုးမြှင့်ပါ။
(၂) ဖော်မြူလာကို ချိန်ညှိပါ၊ ကစီဓာတ်ကုန်ကြမ်းများကို သင့်လျော်စွာ တိုးမြှင့်ကာ အဆီနှင့် ဖိုက်ဘာကုန်ကြမ်းများ၏ အချိုးအစားကို လျှော့ချပါ။
(၃) လိုအပ်ပါက ကော်ထည့်ပါ။(ဆိုဒီယမ်အခြေခံ bentonite slurry)
(၄) Compression Ratio ကို မြှင့်တင်ပါ။လက်စွပ်သေတယ်။
(၅) ကောင်းစွာ ကြိတ်ချေမှုအား ထိန်းညှိပေးသည်။
၄၊ အမှုန်များတွင် အမှုန့်ပါဝင်မှု အလွန်အကျွံ
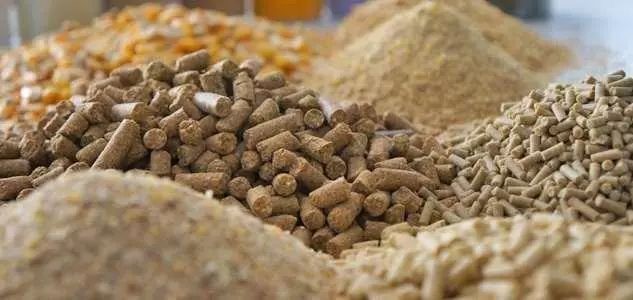
1. အအေးခံပြီးနောက်နှင့် စစ်ဆေးခြင်းမပြုမီ အထွေထွေအစာ၏ အသွင်အပြင်ကို သေချာစေရန် ခက်ခဲသည်။အမှုန်အမွှားများတွင် ပြာများနှင့် အမှုန့်များ ပိုရှိနေကြောင်း ဖောက်သည်များက အစီရင်ခံကြသည်။အထက်ဖော်ပြပါ ခွဲခြမ်းစိတ်ဖြာမှုအပေါ် အခြေခံ၍ ဤအရာအတွက် အကြောင်းရင်းများစွာရှိသည်ဟု ကျွန်ုပ်ထင်သည်-
A. အမှုန်မျက်နှာပြင်သည် ချောမွေ့ခြင်းမရှိ၊ ခွဲစိတ်မှုမှာ မသပ်ရပ်ဘဲ၊ အမှုန်များသည် လျော့ရဲပြီး အမှုန့်များထွက်ရှိနိုင်ခြင်း၊
B. အဆင့်သတ်မှတ်ခြင်း စခရင်၊ ပိတ်ဆို့နေသော စခရင်ကွက်ကွက်များ၊ ရော်ဘာဘောလုံးများ ပြင်းထန်စွာ ဝတ်ဆင်မှု၊ မကိုက်ညီသော မျက်နှာပြင်ကွက် အလင်းဝင်ပေါက် စသည်တို့ဖြင့် မပြည့်စုံသော စစ်ဆေးမှု၊
C. ကုန်ချောဂိုဒေါင်တွင် ပြာအကြွင်းအကျန်များ အများအပြားရှိနေသဖြင့် ရှင်းလင်းမှု မစေ့စပ်ပါ။
D. ထုပ်ပိုးခြင်းနှင့် အလေးချိန်အတွင်း ဖုန်မှုန့်များကို ဖယ်ရှားရာတွင် လျှို့ဝှက်အန္တရာယ်များ ရှိပါသည်။
ကိုင်တွယ်ဆောင်ရွက်မှုများ-
A. ဖော်မြူလာဖွဲ့စည်းပုံကို ပိုမိုကောင်းမွန်အောင်ပြုလုပ်ပါ၊ လက်စွပ်ကို ကျိုးကြောင်းဆီလျော်စွာ ရွေးချယ်ကာ ဖိသိပ်မှုအချိုးကို ကောင်းမွန်စွာထိန်းချုပ်ပါ။
B. granulation လုပ်ငန်းစဉ်အတွင်း၊ ကုန်ကြမ်းများကို အပြည့်အဝရင့်မှည့်ရန်နှင့် ပျော့ပျောင်းစေရန် အပူချိန်၊ အစာကျွေးသည့်ပမာဏနှင့် granulation အပူချိန်တို့ကို ထိန်းချုပ်ပါ။
ဂ။ အမှုန်အမွှားဖြတ်ပိုင်းကို သပ်သပ်ရပ်ရပ်ဖြစ်စေပြီး သံမဏိအမြှေးပါးဖြင့်ပြုလုပ်ထားသော ပျော့ပျောင်းသောဖြတ်တောက်သည့်ဓားကို အသုံးပြုပါ။
D. အဆင့်သတ်မှတ်ခြင်းစခရင်ကို ချိန်ညှိပြီး ထိန်းသိမ်းပါ၊ ကျိုးကြောင်းဆီလျော်သော မျက်နှာပြင်ဖွဲ့စည်းပုံကို အသုံးပြုပါ။
E. ကုန်ချောဂိုဒေါင်အောက်တွင် ဆင့်ပွားစစ်ဆေးခြင်းနည်းပညာကို အသုံးပြုခြင်းသည် အမှုန့်ပါဝင်မှုအချိုးကို လျှော့ချနိုင်သည်။
F. ကုန်ချောဂိုဒေါင်နှင့် ဆားကစ်များကို အချိန်မီရှင်းလင်းရန် လိုအပ်ပါသည်။ထို့အပြင်၊ ထုပ်ပိုးခြင်းနှင့်ဖုန်မှုန့်ဖယ်ရှားရေးကိရိယာကိုတိုးတက်ရန်လိုအပ်သည်။ဖုန်မှုန့်များကို ဖယ်ရှားရန်အတွက် အနုတ်လက္ခဏာဖိအားကို အသုံးပြုခြင်းသည် အကောင်းဆုံးဖြစ်ပြီး၊ ၎င်းသည် ပိုမိုသင့်လျော်သည်။အထူးသဖြင့် ထုပ်ပိုးမှုလုပ်ငန်းစဉ်အတွင်း ထုပ်ပိုးမှုလုပ်သားသည် ထုပ်ပိုးမှုစကေး၏ကြားခံ hopper မှ ဖုန်မှုန့်များကို ပုံမှန်ခေါက်ပြီး သန့်ရှင်းသင့်သည်။.
၅၊ အမှုန်အမွှားအလျား ကွဲပြားသည်။
1. နေ့စဉ်ထုတ်လုပ်မှုတွင်၊ အထူးသဖြင့် 420 အထက်မော်ဒယ်များအတွက် ထိန်းချုပ်ရန်အခက်အခဲများကို ကြုံတွေ့ရလေ့ရှိပါသည်။ ၎င်းအတွက် အကြောင်းရင်းများကို အကြမ်းဖျင်းအားဖြင့် အောက်ပါအတိုင်း အကျဉ်းချုံးဖော်ပြထားပါသည်။
(၁) granulation အတွက် အစာကျွေးသည့် ပမာဏသည် မညီမညာဖြစ်ပြီး အပူပေးသည့် အကျိုးသက်ရောက်မှုသည် အလွန်ပြောင်းလဲပါသည်။
(၂) မှိုကြိတ်စက်များ သို့မဟုတ် လက်စွပ်မှိုနှင့် ဖိအားကြိတ်စက်များ၏ ပြင်းထန်စွာ ပတ်တီးမှုကြားတွင် ကွာဟချက်။
(၃) လက်စွပ်မှို၏ axial direction တစ်လျှောက်၊ အစွန်းနှစ်ဖက်စလုံးရှိ discharge speed သည် အလယ်တွင်ရှိသောထက်နိမ့်ပါသည်။
(၄) လက်စွပ်မှို၏ အပေါက်ကို ဖိအားလျှော့ချခြင်းသည် ကြီးလွန်းပြီး အဖွင့်နှုန်းလည်း မြင့်မားသည်။
(၅) ခုတ်ဓား၏ အနေအထားနှင့် ထောင့်သည် ကျိုးကြောင်းဆီလျော်မှုမရှိပါ။
(၆) Granulation အပူချိန်။
(၇) ကြိုးဝိုင်း၏ အမျိုးအစားနှင့် ထိရောက်မှု အမြင့် (ဓါးအနံ၊ အနံ) သည် ကြိုးဝိုင်းအတွင်း သက်ရောက်မှုရှိသည်။
(၈) တစ်ချိန်တည်းတွင်၊ compression chamber အတွင်းရှိ ကုန်ကြမ်းများ ဖြန့်ဖြူးမှုမှာ မညီမညာဖြစ်နေသည်။
2. အစာနှင့် အစေ့များ၏ အရည်အသွေးကို ၎င်းတို့၏ အတွင်းပိုင်းနှင့် ပြင်ပ အရည်အသွေးများအပေါ် အခြေခံ၍ ယေဘုယျအားဖြင့် ခွဲခြမ်းစိတ်ဖြာပါသည်။ထုတ်လုပ်မှုစနစ်တစ်ခုအနေဖြင့်၊ ကျွန်ုပ်တို့သည် အစာအမှုန့်များ၏ ပြင်ပအရည်အသွေးနှင့် ဆက်စပ်သောအရာများကို ပိုမိုထိတွေ့ခွင့်ရပါသည်။ထုတ်လုပ်မှုရှုထောင့်မှကြည့်လျှင် ရေနေအစာစေ့များ၏ အရည်အသွေးကို ထိခိုက်စေသည့် အချက်များ ကို အောက်ပါအတိုင်း အကြမ်းဖျင်း အကျဉ်းချုံးနိုင်သည်။
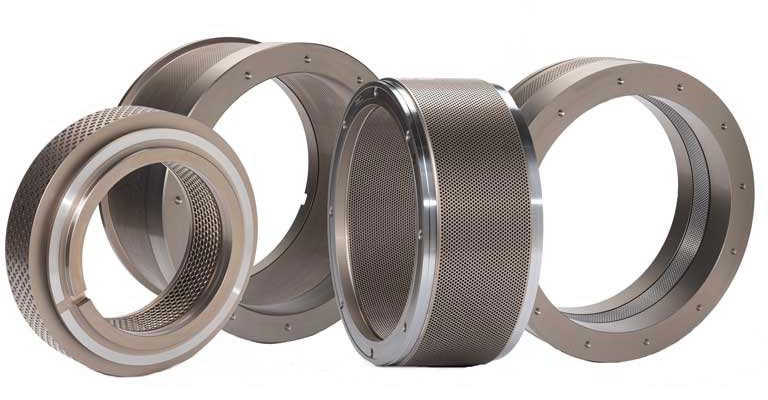
(၁) ဖော်မြူလာများ၏ ဒီဇိုင်းနှင့် ဖွဲ့စည်းမှုသည် ရေနေအစာအစာစေ့များ၏ အရည်အသွေးအပေါ် တိုက်ရိုက်သက်ရောက်မှုရှိပြီး စုစုပေါင်း၏ ၄၀ ရာခိုင်နှုန်းခန့်၊
(၂) ကြိတ်ခွဲခြင်း၏ ပြင်းထန်မှုနှင့် အမှုန်အရွယ်အစား တူညီမှု၊
(၃) လက်စွပ်မှို၏ အချင်း၊ ဖိသိပ်မှုအချိုးနှင့် မျဉ်းဖြောင့်အလျင်သည် အမှုန်များ၏ အရှည်နှင့် အချင်းအပေါ် သက်ရောက်မှုရှိသည်။
(၄) လက်စွပ်မှို၏ ဖိသိပ်မှုအချိုး၊ မျဉ်းဖြောင့်အလျင်၊ မီးငြှိမ်းသတ်ခြင်းနှင့် အပူဒဏ်ခံနိုင်မှု၊
(၅) ကုန်ကြမ်းများ၏ အစိုဓာတ်ပါဝင်မှု၊ အပူဒဏ်၊ အအေးခံခြင်းနှင့် အခြောက်ခံခြင်းသည် ကုန်ချောများ၏ အစိုဓာတ်ပါဝင်မှုနှင့် အသွင်အပြင်အပေါ် သက်ရောက်မှုရှိသည်။
(၆) စက်ကိရိယာများကိုယ်တိုင်၊ လုပ်ငန်းစဉ်ဆိုင်ရာအချက်များနှင့် ငြှိမ်းသတ်ခြင်းနှင့် အပူပေးခြင်းဆိုင်ရာ သက်ရောက်မှုများသည် အမှုန်အမွှားပါဝင်မှုအပေါ် သက်ရောက်မှုရှိသည်။
3. ကိုင်တွယ်ဆောင်ရွက်မှုများ-
(၁) အထည်ခြစ်ရာ၏ အလျား၊ အနံနှင့် ထောင့်ကို ချိန်ညှိပြီး စုတ်ပြဲနေသောခြစ်ရာကို အစားထိုးပါ။
(၂) အစာကျွေးသည့်ပမာဏနည်းပါးခြင်းကြောင့် အစပိုင်းနှင့် ထုတ်လုပ်မှုပြီးဆုံးခါနီးတွင် ဖြတ်တောက်ထားသော ဓါးများ၏ အနေအထားကို အချိန်မီ ချိန်ညှိရန် ဂရုပြုပါ။
(၃) ထုတ်လုပ်မှုလုပ်ငန်းစဉ်အတွင်း တည်ငြိမ်သောအစာနှုန်းနှင့် ရေနွေးငွေ့ပေးဝေမှုကို သေချာစေပါ။ရေနွေးငွေ့ဖိအားနည်းပြီး အပူချိန်မတက်လာပါက၊ အချိန်မီ ချိန်ညှိခြင်း သို့မဟုတ် ရပ်တန့်သင့်သည်။
(၄) ကွာဟချက်ကို ကျိုးကြောင်းဆီလျော်စွာ ချိန်ညှိပါ။roller ခွံ.မှိုအသစ်ကို ဒလိမ့်တုံးအသစ်ဖြင့် လိုက်နာပါ၊ ဝတ်ဆင်မှုကြောင့် ဖိအားကြိတ်စက်နှင့် လက်စွပ်မှိုများ၏ မညီညာသောမျက်နှာပြင်ကို ချက်ခြင်းပြုပြင်ပါ။
(၅) လက်စွပ်မှို၏ လမ်းညွှန်အပေါက်ကို ပြုပြင်ပြီး ပိတ်ဆို့နေသော မှိုပေါက်ကို ချက်ချင်း သန့်ရှင်းပါ။
(၆) လက်စွပ်မှိုကို မှာယူသောအခါ၊ မူလလက်စွပ်ပုံစံ၏ axial direction ၏ အစွန်းနှစ်ဖက်ရှိ အပေါက်သုံးတန်း၏ ဖိသိပ်မှုအချိုးသည် အလယ်တွင် ထိုထက် 1-2 မီလီမီတာ သေးငယ်နိုင်သည်။
(၇) အထူ 0.5-1mm အကြား ထိန်းချုပ်ထားသော အပျော့စား ဓားကို အသုံးပြု၍ ကွင်းမှိုနှင့် ဖိအားကြိတ်စက်ကြားရှိ ကန့်လန့်ဖြတ်မျဉ်းပေါ်တွင် အတတ်နိုင်ဆုံး ချွန်ထက်သော အစွန်းများ ရှိစေရန်၊
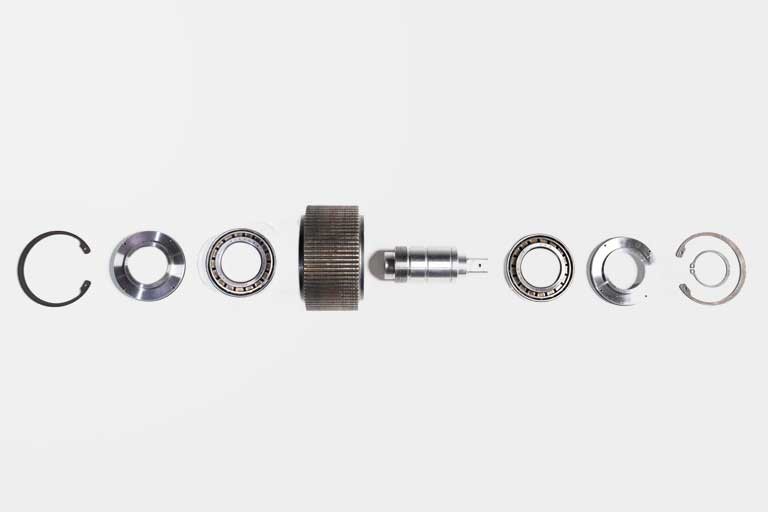
(၈) လက်စွပ်မှို၏ အလယ်ဗဟိုကို သေချာစစ်ဆေးပါ၊ granulator ၏ spindle clearance ကို ပုံမှန်စစ်ဆေးပြီး လိုအပ်ပါက ချိန်ညှိပါ။
၆၊ အနှစ်ချုပ် ထိန်းချုပ်ရေးအချက်များ
1. ကြိတ်ခြင်း- ကြိတ်ခွဲခြင်း၏ ချောမွေ့မှုကို သတ်မှတ်ချက်လိုအပ်ချက်များနှင့်အညီ ထိန်းချုပ်ရပါမည်။
2. ရောစပ်ခြင်း- သင့်လျော်သော ရောစပ်သည့်ပမာဏ၊ ရောစပ်ချိန်၊ အစိုဓာတ်ပါဝင်မှုနှင့် အပူချိန်တို့ကို သေချာစေရန်အတွက် ကုန်ကြမ်းရောစပ်ခြင်း၏ တူညီမှုကို ထိန်းချုပ်ရပါမည်။
3. ရင့်ကျက်မှု- puffing machine ၏ ဖိအား၊ အပူချိန်နှင့် အစိုဓာတ်ကို ထိန်းချုပ်ရပါမည်။
အမှုန်အမွှားပစ္စည်း၏ အရွယ်အစားနှင့် ပုံသဏ္ဍာန်- compression မှိုများနှင့် ဖြတ်တောက်ထားသော ဓါးသွားများ၏ သင့်လျော်သော သတ်မှတ်ချက်များကို ရွေးချယ်ရပါမည်။
5. အချောထည်အစာ၏ ရေပါဝင်မှု- အခြောက်ခံခြင်းနှင့် အအေးခံချိန်နှင့် အပူချိန်ကို သေချာစေရန် လိုအပ်ပါသည်။
6. ဆီဖြန်းခြင်း- တိကျသော ဆီဖြန်းမှုပမာဏ၊ nozzles အရေအတွက်နှင့် ဆီအရည်အသွေးကို ထိန်းချုပ်ရန် လိုအပ်ပါသည်။
7. စစ်ဆေးခြင်း- ပစ္စည်း၏ သတ်မှတ်ချက်များအရ ဆန်ခါအရွယ်အစားကို ရွေးချယ်ပါ။
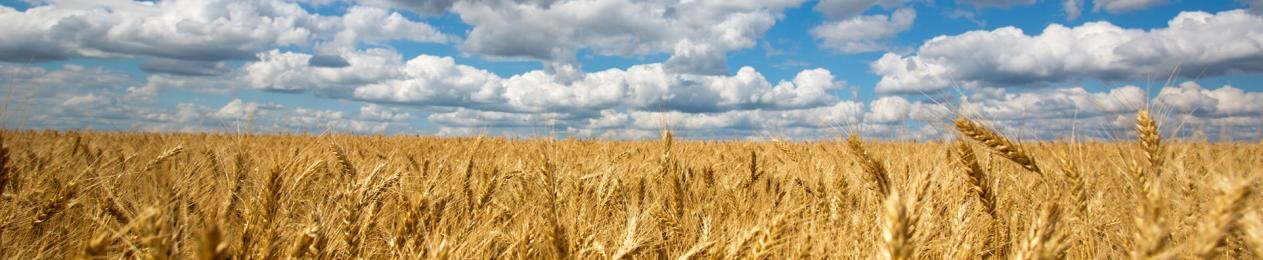
စာတိုက်အချိန်- နိုဝင်ဘာ-၃၀-၂၀၂၃